Company
anniversary:
50 years of Interflex
Learn more about events, products, and successes in our company’s history. Get to know the people behind the brand and take a glimpse at our vision for the future.
From flextime pioneer to provider of New Work solutions
Unlocking the power of numbers
New Work and work-life balance: many people view these terms as meaning flexible, self-determined work from anywhere, anytime. This concept has been around for a while now. Here at Interflex, we’ve been working to add flexibility to working time for 50 years now through technological solutions, giving millions of employees more personal responsibility – now and into the future. That’s because people are at the heart of everything we do.
We started out as a pioneer in time recording, and today, we are a full-spectrum provider of workforce management and security solutions having to do with access control and visitor management, with our own hardware, software and in-house services.

The early days of Interflex: Willi Haller
Wilhelm (“Willi”) Haller was a thought leader and pioneer in flextime, as the concept was first called in the 1960s. A businessman from Germany’s region of Swabia, he went on to become the founder of Interflex. Haller developed the first electromechanical time recording devices, which were based on industrial counters. The goal was to make it possible to record the hours actually worked by employees, making their work schedules more flexible. Experts told him it couldn’t be done. But he proved them wrong!
His view was that flexible working hours would make employees responsible partners in scheduling, so they would be happy with their work. Another objective was to adjust people’s working hours to match actual workloads. Flexible working hours, logged systematically, improved cost-effectiveness at the company due to optimized scheduling of full-time and part-time workers. Rigid working hours, by contrast, brought overloading, absences, and costly work backlogs.
Haller firmly believed flextime would be an important tool for securing employees’ loyalty in times when skilled workers were in short supply. That was a well-known argument then as now.
Milestones in the 50-year history of Interflex
Together with our customers, we have achieved significant milestones over our history. Check out the graphic for interesting facts about our company history.
Interflex has been a successful market player since 1974, offering a diverse range of solutions
Our systems are used to manage some 5.8 million employees a day
More than 500 employees are involved within Interflex Datensysteme GmbH, for example

From pioneers to innovators:
The inspiring history of Interflex
Take a journey through the fascinating world of Interflex, a company that has made history and more – it has also been instrumental in shaping the present and future of time recording and access control. From pioneering beginnings to worldwide success, Interflex has come a long way – through it all, always creating solutions that put people first.
The Interflex logo over time
Each logo has a story to tell, and each one is also an expression of the alignment and design trends at the time. The identity of the Interflex logo has also changed over the past 50 years, showing how we have grown and changed. Amid all these changes, one visual element has been a constant throughout – the Interflex butterfly, a valued part of who we are right from the start.
1974 1980s 1990s 2000 2013 2016 since 2022
Growing in line with customer requirements
The true measure of our success is how happy our customers are. That has been our credo ever since our company was first founded. We have always focused on doing more than just supplying products. Our goal is to build and maintain valuable partnerships and to grow and learn from every project. We are proud to say that we are more than just a supplier. We’re a trusted partner, and most of our customer relationships have existed for a long time.
What employees say about Interflex
The employees of Interflex are the heart of the company. With tireless commitment and dedication, valuable contributions, and extensive expertise, they do their part each and every day to make sure we can implement projects reliably and celebrate successes. Positive employee feedback shows that Interflex creates the right conditions for a pleasant work environment as a company.
Looking ahead: our vision for the coming 50 years.
Our people will continue to be at the heart of everything we do at Interflex, now and into the future. Now more than ever, the objective across the working world will be to ease the burden on valuable skilled workers and strengthen their personal responsibility with efficient solutions – while also taking their individual life situations into account, in keeping with the concept of New Work. This improves employee loyalty and motivation.
Key aspects include the trend toward collaboration tools in workforce management and the digitalization of HR processes to include employees in working hours planning and support workforce co-determination. These features let employees organize their own working hours from anywhere, using their own smartphone. Interflex offers a native app called teamtime (iOS and Android) to help with this. It focuses on ease of use.
Physical security will grow more and more important going forward as well – and not just due to new cybersecurity regulations like NIS2 and DORA and the German KRITIS Umbrella Act. Security should be viewed holistically, as a mix of digital and physical protective measures.
But with skilled workers in increasingly short supply, security vulnerabilities could also arise if companies lack managers for security and IT. That’s why Interflex is continuing to invest in expanding its cloud services. This helps medium-sized companies in particular, as it means they need fewer staff for on-premise solutions.
A new generation of terminals will also provide added security going forward. Thanks to the new generation, Interflex will be gradually equipping its wired access readers with new security features that have previously been part of the battery-operated lock components in the Opendor product family. In this way, Interflex is supporting many customers’ desire for connected access control and system integration into building and security management systems.
With an eye to the international alignment of Interflex, customers will continue to benefit from further added value and lasting synergies, now and into the future. This is because as part of the Allegion group of companies, Interflex is backed by a strong network of partners, especially in developing and investing in access and security solutions to meet future needs.
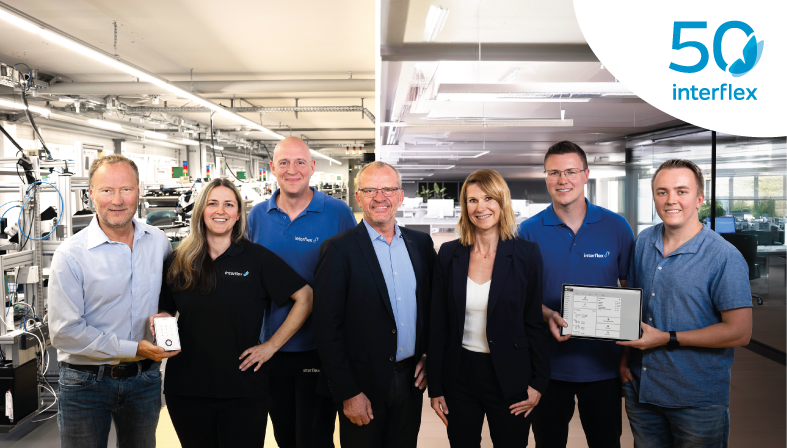
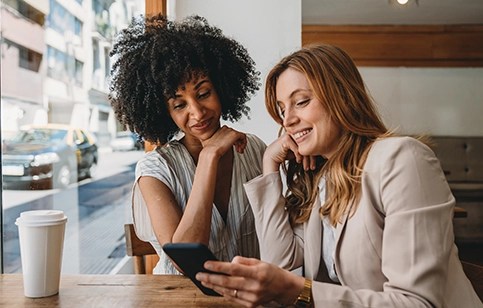
The press kit contains further information about the history of Interflex and the company’s future plans. If you have any questions or would like further information, please do not hesitate to contact us. Please consult the press kit for contact information.